Building climate-resilient housing requires shifting away from timber and trees
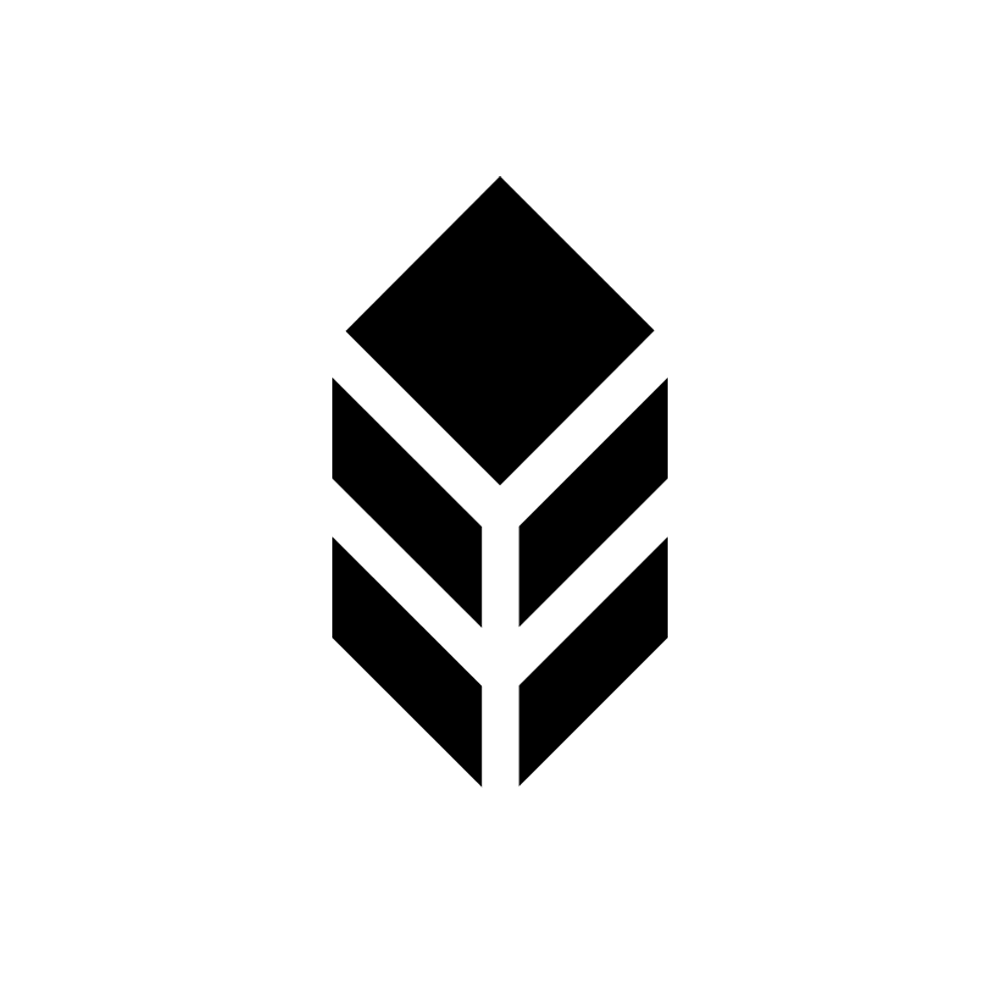
Dan Webb
/
6.29.23
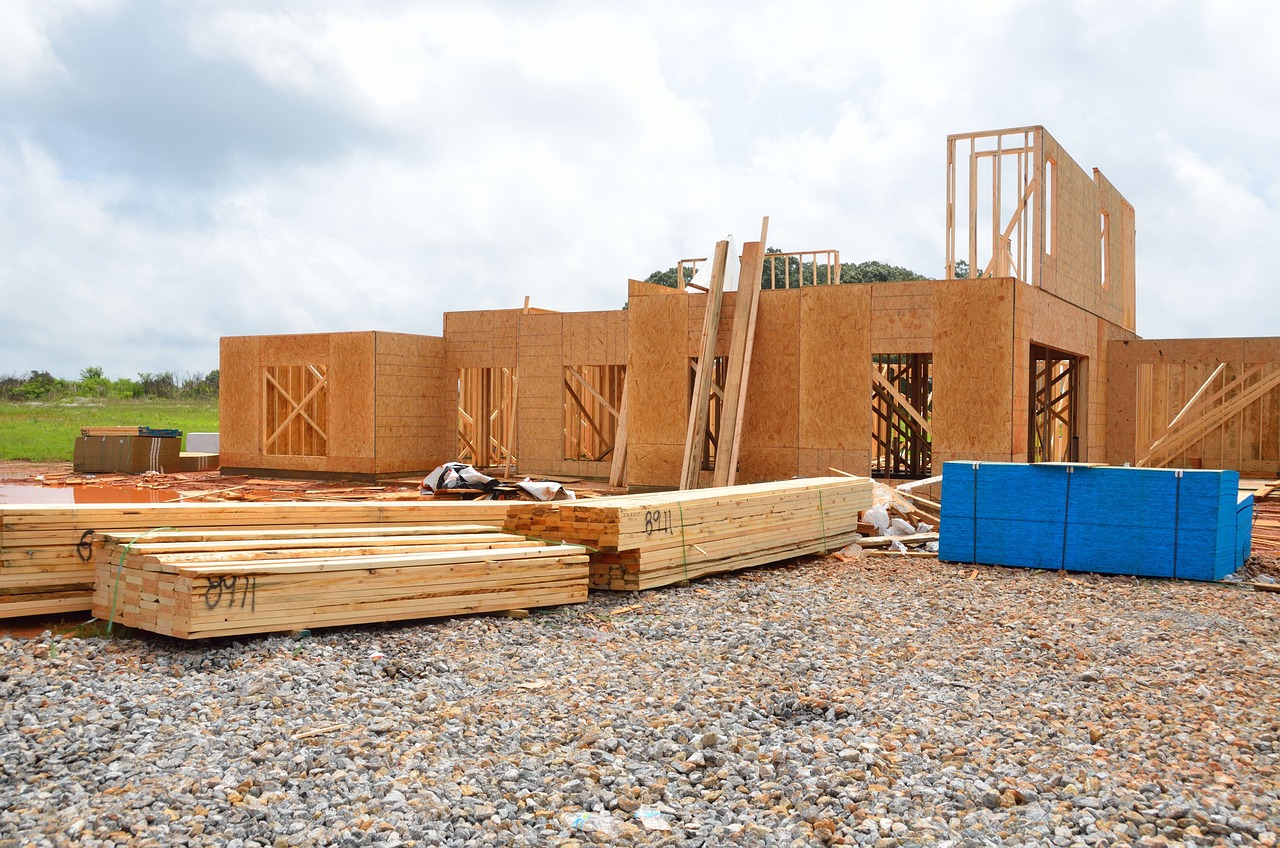
Throughout history, human-made structures have adapted and evolved in response to technological advances and environmental conditions. Humans constructed the first primitive shelters of wood and animal skins. In the modern era, homebuilding materials have become more varied and specialized, yet trees still remain central to how we build.
Over 150 years ago, a disaster dramatically altered the materials builders and architects came to rely upon for urban construction. The Great Chicago Fire of 1871 ignited a massive shift in urban planning as Chicago harnessed new industrial technology to rebuild itself from ashes into an architectural marvel of the 20th century.
This catastrophe cost Chicago residents $222 million, equivalent to $5.5 billion in 2023. Chicago’s construction industry leaders feared that continuing to build with conventional timber would lead to another widespread fire. Consequently, the city adopted more expensive fire-proof construction methods utilizing steel and concrete.
While the events of The Great Chicago Fire affected the urban inhabitants of 1870s Chicago, the adverse effects of climate change disproportionately affect rural and suburban communities in the 21st century.
The Challenge of Climate Change
Unlike The Great Chicago Fire, the wildfires driven by climate change today disproportionately affect the livelihood and structural integrity of suburban and rural homes.
According to the Environmental Defense Fund, climate change creates hot and dry conditions that cause wildfires, which typically spread across the western region of the United States, causing damage to nearby structures. The National Oceanic and Atmospheric Administration (NOAA) estimates that, on average, each wildfire costs the United States $6.4 billion in total losses.
Flooding around waterways such as rivers is equally devastating. Each of these events is estimated to cost the U.S. an average of $4.6 billion. In addition, every hurricane and tropical cyclone cost an average of nearly $22.5 billion.
Wildfires and flooding can also damage managed timberland causing the price of lumber to surge; a financial blow to rural communities that frequently struggle to rebuild after a disaster.
Wood: The Status Quo of Homebuilding and Infrastructure
Other than laying a concrete slab foundation upon which most homes in the U.S. are built, single-family homes are primarily constructed of wood. We build homes with timber framing (two-by-fours and two-by-sixes) and engineered wood products like Oriented Strand Board (OSB) and plywood for wall sheathing, roof decking, and subflooring. Very often, tree-based materials are not resilient to the effects of extreme weather events such as hurricanes, flooding, and wildfires, which are amplified in magnitude by our changing climate.
Harvesting and producing timber products is not a sustainable practice. Though wood products can store carbon and increasingly replace emission-intensive building materials such as concrete and steel, timber production emits significant carbon emissions, from the tree farm to the production plant to the finished product. According to the Center for Sustainable Economy, the logging industry in North Carolina emits 44 million tonnes of carbon a year, making the industry the 3rd largest greenhouse gas producer in the state.
Wood fails to provide adequate protection against the effects of climate change while at the same time contributes to the intensification of climate change.
Climate Resilient and Sustainable Housing
To reduce climate change impacts, the housing and construction industries are moving toward building more resilient infrastructure that integrates and relies upon sustainable materials and technologies. There are several ways to build a home to be more resilient to climate change, but here are a few examples:
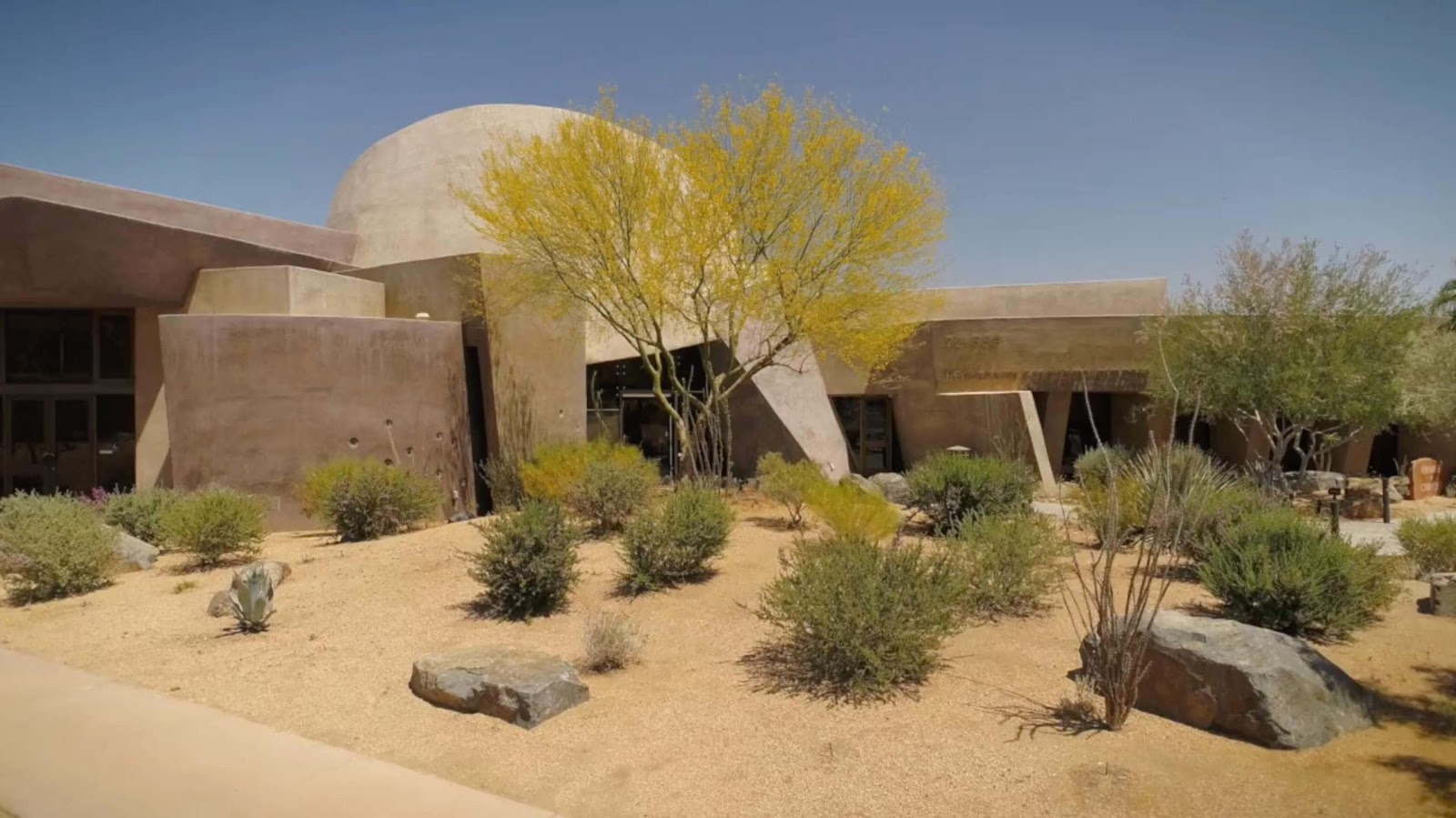
An example of housing that can withstand climate change:
Featured on CNBC and ProBuilder, Re-Structure Group (RSG) makes a climate-resilient building system called 3-D that combines the insulation of Structural Insulated Panels (SIPs) with structural reinforcements made of steel and other human-engineered materials. RSG combines these technologies into a three-dimensional building panel used to build residential, commercial, and industrial buildings.
By avoiding flammable materials in their production, RSG asserts that their structural panels are both fire-resistant and fireproof. RSG further claims the three-dimensional structural package can protect homes and buildings from other climate-related weather events such as earthquakes, hurricanes, and wildfires.
Products like RSG’s 3-D panels are not yet present in modern building construction. Still, they could become valuable materials for areas at high climate-related weather risk due to their rigid design enabling homes to withstand the forces of nature.
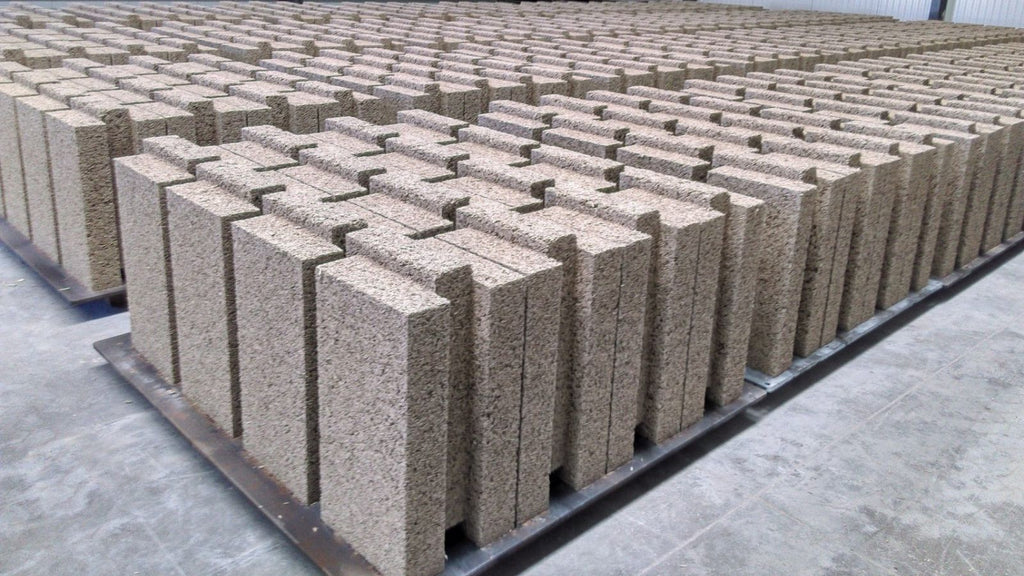
An example of housing that contributes to climate restoration:
New building materials are incorporating plants into construction in innovative ways. One example is hempcrete, a plant-based replacement for concrete. This material is cast into walls and slabs or pre-manufactured as blocks and bricks.
Local building codes and regulatory processes are challenges for companies working with new materials. Because their products are made from hemp and limestone, companies like Hempitecture have faced challenges in achieving fireproof or fire-resistant status. In 2020, Hempitecture became the first company to receive a perfect score for a hemp-based concrete product in ASTM fire testing in the United States.
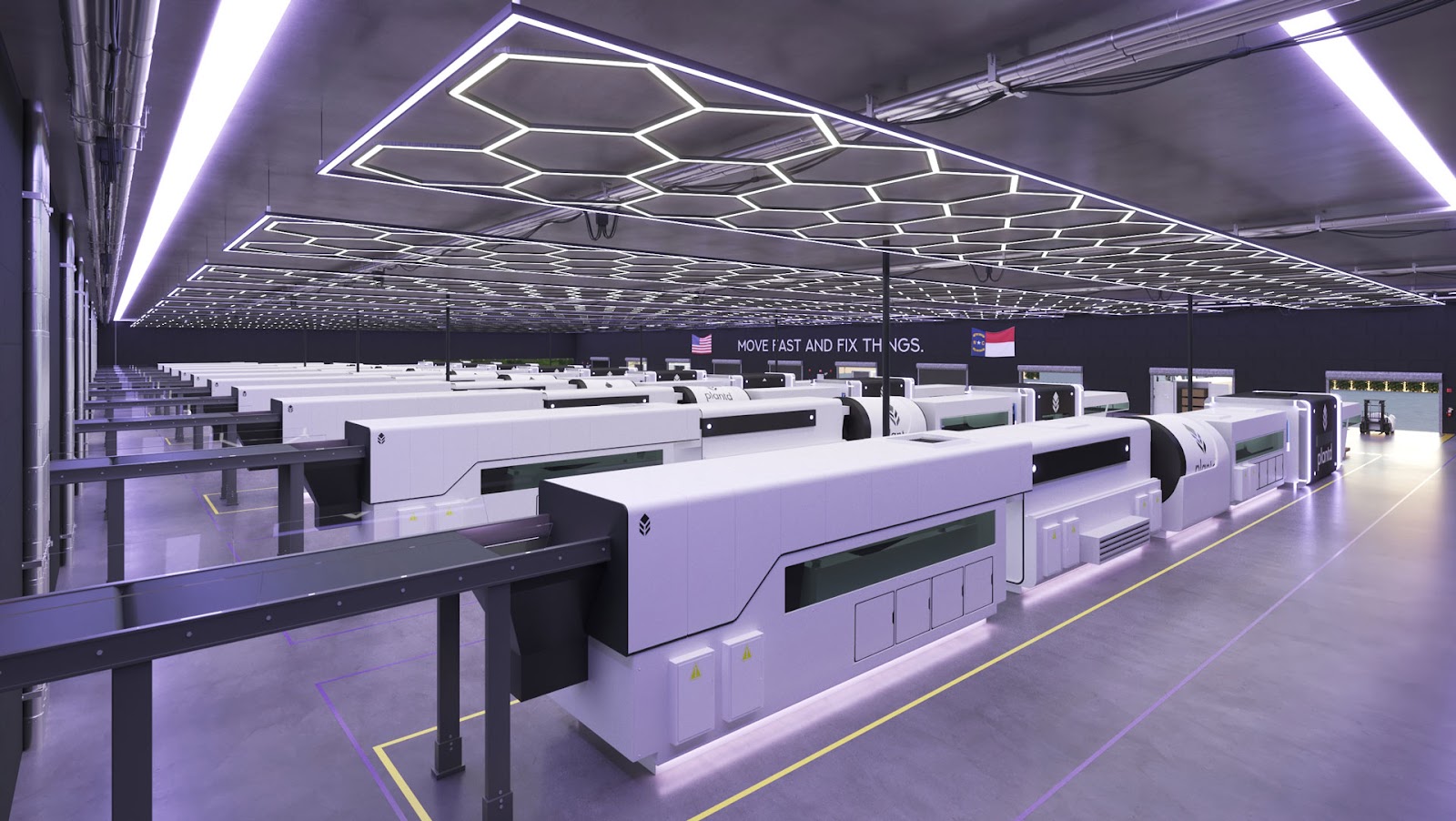
An example of housing that withstands climate change and contributes to climate restoration:
At Plantd, we are revolutionizing the timber industry by creating new products that outperform wood-based products in both resilience and sustainability.
We start by eliminating fossil fuels from our manufacturing process by building the world’s first 100% electric-powered automated assembly line for engineered building panels. Next, we cultivate tall, rapidly-renewable perennial grass that captures significant amounts of carbon dioxide and uses 9x less land than trees. Then we transform this plant into durable and valuable building materials that outperform their wood-based counterparts.
By placing a rapidly-renewable raw material through a low-emissions production process, our product offsets carbon dioxide emissions instead of producing emissions. We capture carbon dioxide naturally and transform it into a useful building material with resilient and climate-restorative properties.
We are creating the future of homebuilding materials: one that stands in balance with nature–– for everyone.